In a world where mass-produced furniture dominates the market, owning furniture that reflects your unique style and personality can feel like searching for a needle in a haystack. Bespoke furniture offers the opportunity to have something that reflects your individuality; where every curve, every detail, is tailored to perfection.
In this case study, we explore the intricacies involved in crafting bespoke Demi-lune cabinets, tailored to meet the exacting standards of a discerning client. Demi-lune cabinets, with their graceful curves and exquisite craftsmanship, represent a pinnacle of fine furniture design and craftsmanship.
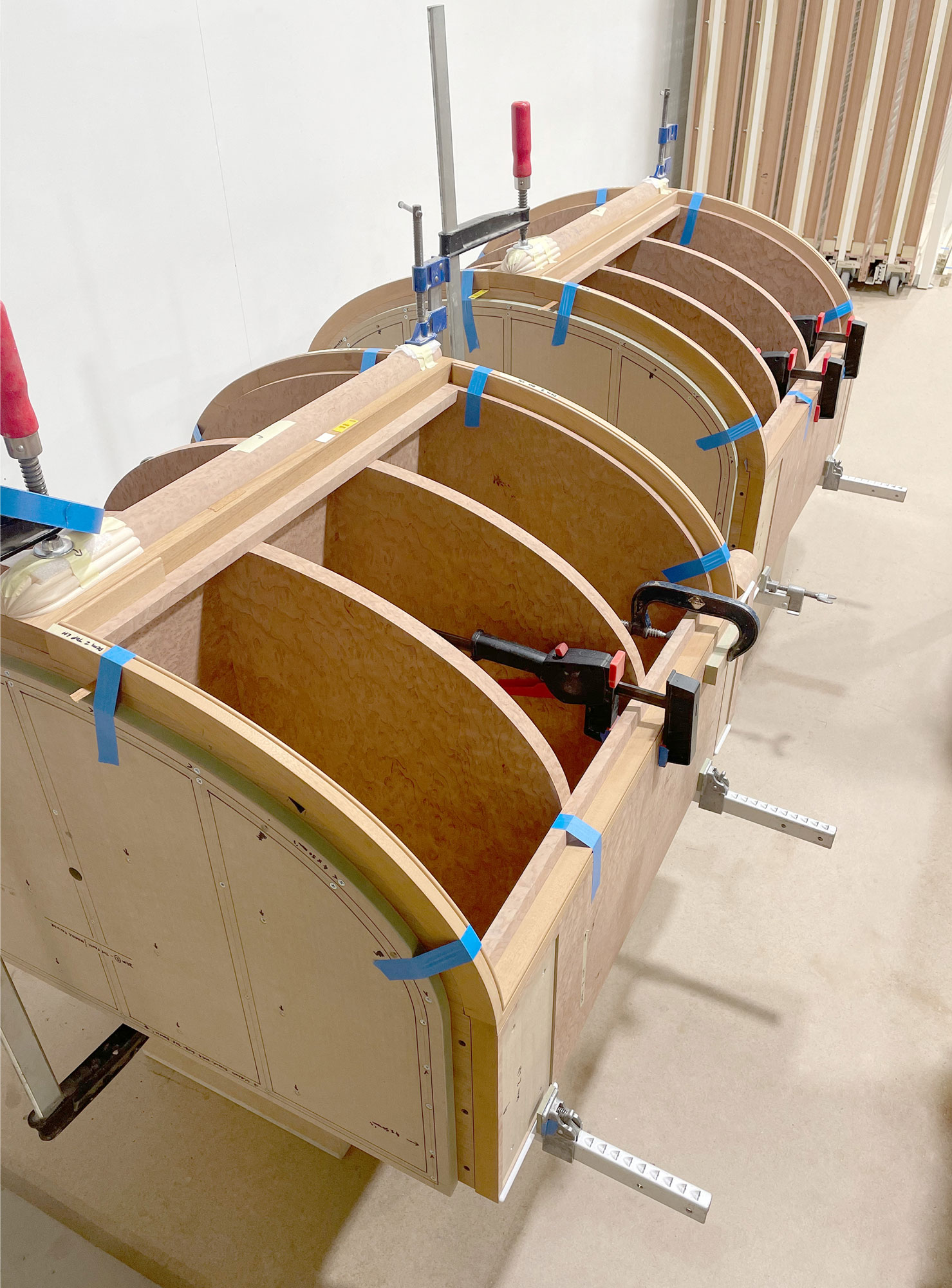
The Brief:
To design cabinets that not only met the client’s aesthetic needs, but also seamlessly integrated into the fabric of the building.
The journey began with a collaborative effort with Markham Roberts Design and Lauren Pittams Senior Project Manager at NEJ Stevenson alongside Josh Cosh Hall (Senior Cabinet Maker), Richard Evans (Senior Cabinet Maker) and Mark Clemson (Head of Spray Shop) – tailoring the initial client design, ensuring it not only captured the vision but also considered the practical aspects of construction and finishes. Two of the Demi-lunes were to conceal air-conditioning units, requiring innovative solutions to blend them seamlessly into the construction.
One of the key elements in realising the client’s vision was the careful selection of materials. With the client’s input and inspiration images, the team decided on Vavona Burr and Brazilian Mahogany. To create a suitable substructure the curved doors were formed from Birch Ply. The curved details from Limewood and the carcass from MDF and Raku.
In keeping with the functional requirements of the air-conditioning units they featured bespoke grilles which were developed by our team to help with the efficient circulation of the air throughout the room.
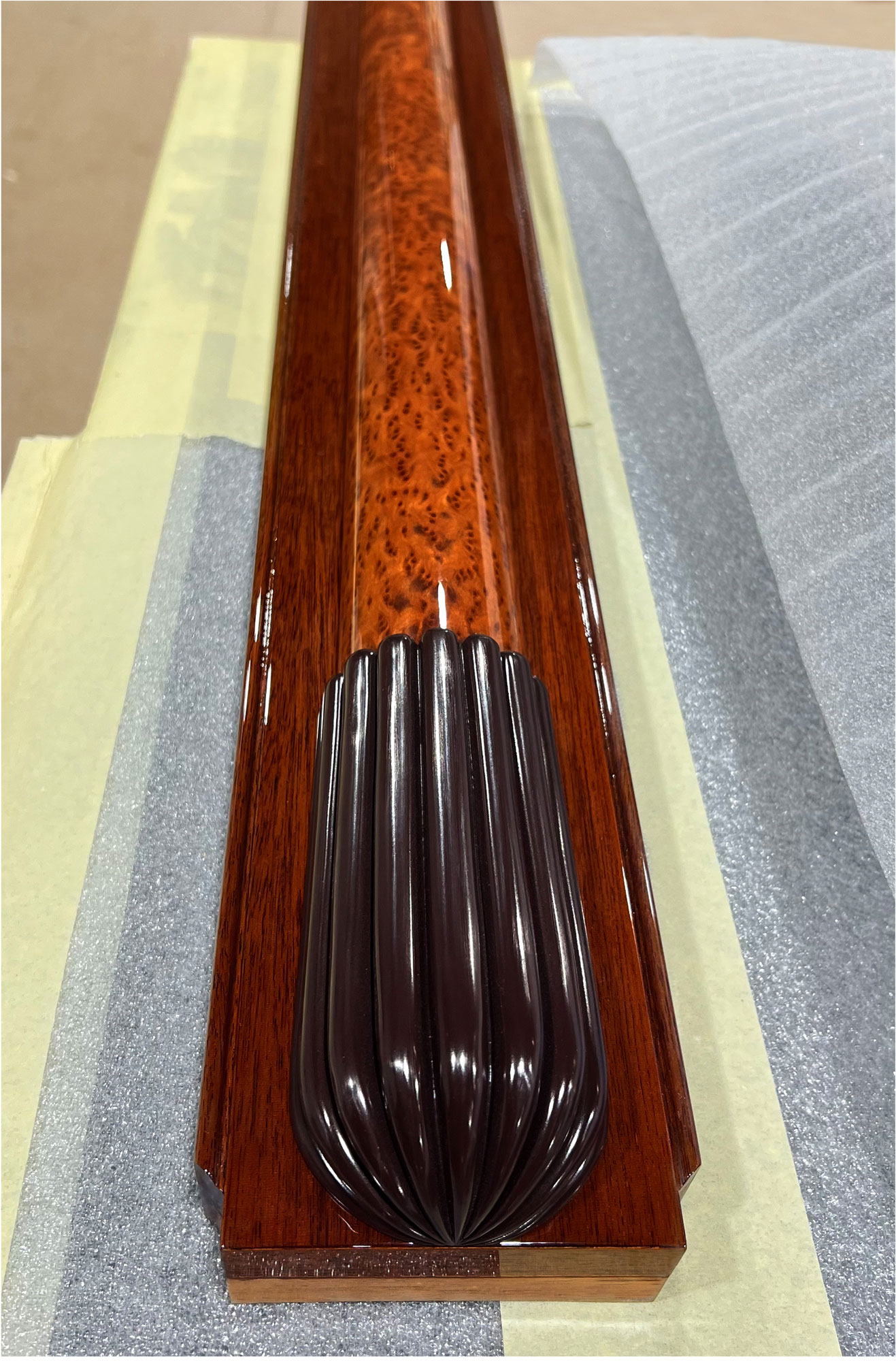
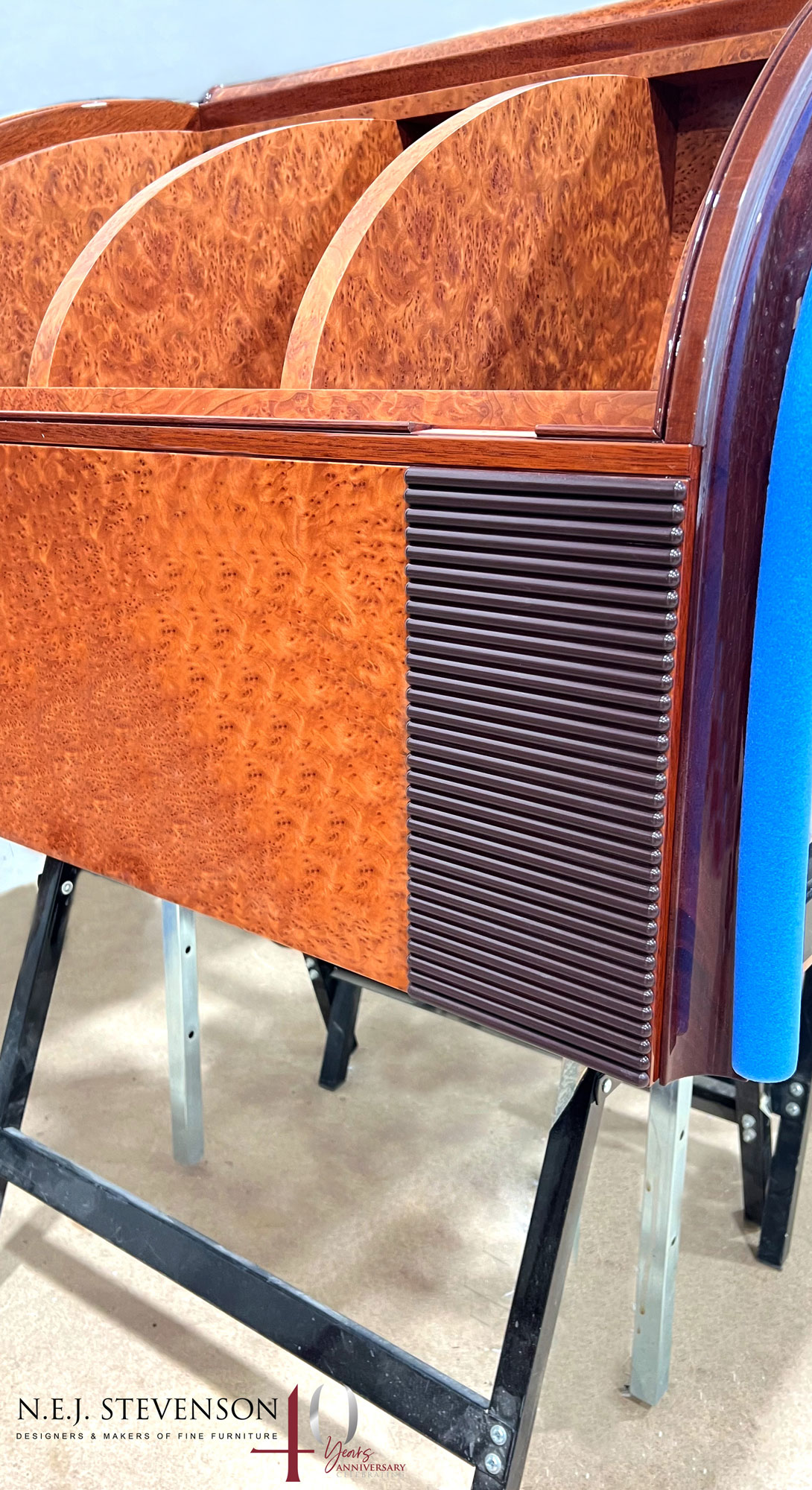
The Crafting Process:
The process commenced with CNC machining of the main cabinetry components. Significant focus was placed on the veneer work, with Josh Cosh Hall spearheading the meticulous selection and application of veneers to achieve seamless continuity in pattern and texture.
Crafting the signature curved doors was no small feat. Using a Curvomatic jig, the team shaped 1.5mm laminates with precision, ensuring that the curve held true to form. An initial sample was made to ensure that the curve held the radius, and a blank was produced from which the makers could work.
Richard Evans led the construction of the cabinets, overseeing the incorporation of intricate details such as finger mouldings and curved feet. Assembling the cabinets proved to be a test, particularly in fitting the front and central legs onto curved frames. The front profile of the cabinet needed to taper from the top to the bottom into a conical shape. Richard and Josh were able to tackle this issue and come with innovative solution to achieve the desired effect.
Fitting the front and central legs onto curved frames posed additional challenges, requiring meticulous attention to detail. Issues such as positioning of raised elements and mitring back onto themselves were addressed through team discussions and collaborative effort.
Hanging curved inset doors on butt hinges is a true test of skill made easier by the meticulous attention to build the carcases perfectly true in all planes, emphasising the precision required in cabinetmaking. The oval top mouldings were machined over several months, allowing for timber settling and ensuring structural integrity.
The final stages of the manufacturing process involved meticulous sanding, spraying, and lacquering, culminating in the reassembly of the cabinets to perfection. This project was not just about making furniture; it was a testament to the power of teamwork and collaboration, as two lead cabinetmakers came together to bring the client’s vision to life.
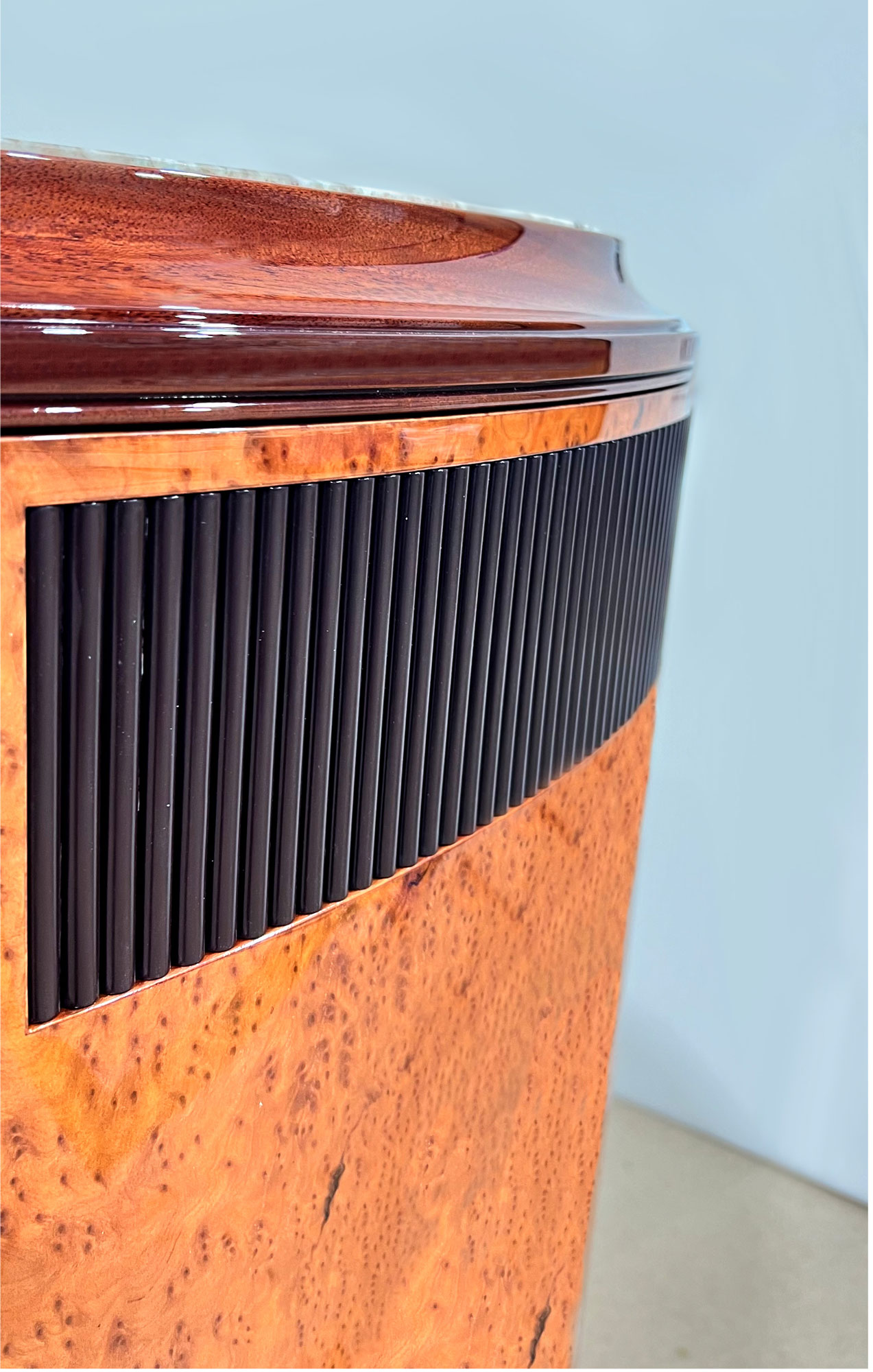